Not everyone in manufacturing roles has a lot of experience with Lean or OEE. In fact, here we are nearly 40 years after OEE was first described in Introduction to TPM: Total Productive Maintenance, and people are still asking how to calculate OEE. Everyone has a story about how they learned about OEE and Lean, including me. What’s fascinating is that despite all that’s been written on these topics, manufacturing companies still struggle to capture significant value from Lean tools and OEE calculations.
It was the early 2000s; I was fresh out of Six Sigma Black Belt training, and a fellow student told me about something I'd never heard of before — Lean Manufacturing. I was intrigued and immediately purchased The Machine that Changed the World, which indeed changed my world. The book turned my thinking upside down and it was a true philosophical awakening: Understand what is valuable and what is not, and engage those who do the work in improving their work. So simple, so elegant. I wanted in!
Accurate OEE Calculation Revealed (Painful) Reality
A short time later, I attended a Lean seminar. The stories about standard work, and the before and after pictures showing 5S transformations were fascinating. However, the most powerful learning was the introduction to OEE. The presentation revealed that OEE is a way to measure productivity in an absolute sense, remove perceptions about what we "think" we should be producing, and force manufacturing companies to understand what they can actually produce. The instructor explained that 85% OEE is typically considered world class manufacturing.
Even before I heard about the OEE formula, I was proud of the manufacturing site where I worked. We had a production line that everyone acknowledged as running very well; in fact, it always beat standard. As soon as I learned how to calculate OEE, I wanted to know what it was for that line, expecting at least 65%. I ran the OEE calculation, and was flummoxed when the math said about 35%. How could that be? I double-checked my understanding of the calculation, and my numbers — even though I wanted it to be higher, it was still 35%. I was confused — How could we be that low and not even know it? How could we have all that extra capacity that was invisible to us? And most concerning, how could I go back to my company, introduce this new operational metric, describe its value, and then report our best line was at 35%?
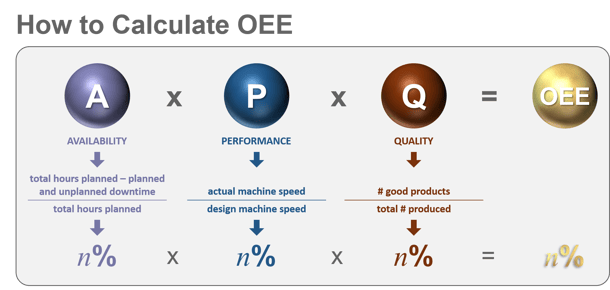
Eager to Use OEE to Drive Improvement
As I started to educate the organization on both the concept and our current OEE, there was disbelief and frustration. No one wants to hear they’re not as good as they think. Despite those feelings, company and plant leadership were willing to give it a try. We struggled a lot to integrate OEE into our thinking and operations, until business changes drove the need for drastic improvement. At that point, the company implemented a production tracking system, which gave us real-time visibility of our issues. Our OEE was staring right back at us all the time — there was no hiding from the fact we had a lot of opportunities for improvement.
Our engineers got excited, but operations teams still didn't seem to get it … OEE flat out didn't resonate. The operations leaders talked with the operators and amongst ourselves, and grappled with the problem of why shop floor workers weren’t on the same page with managers and supervisors. You’ve probably already guessed what the problem was — lack of change management.
Thinking back, we realized that as soon as the OEE calculation was available, we immediately switched targets to OEE instead of case count, which had been the measuring stick for years. The about-face didn’t take into account the operators; we changed the benchmark to something that was still confusing to them, and in this we hadn't shown them the proper respect. Quite simply, we neglected to give our people enough time or education to understand the manufacturing metric and what affects it.
Course Correction: Building a Lean Culture
To get back on track we decided to include a metric that had always been meaningful to the operators them plus provide more education on the new productivity metric. By pulling back and measuring both OEE and case count, everyone was satisfied, and it gave the operators time to make the correlation. Guess what — creating a lean culture and measuring both worked!
Ultimately, we provided data from the production tracking system to an educated and fully engaged workforce. We also set clear goals and created a tiered structure to review our performance versus the improvement targets, which paved the way for significant improvement. When everything fell into place, we started winning and work became fun. That plant was consistently breaking production records.
The most powerful learning along the way wasn’t specifically lean six sigma principles or what OEE stands for, although those are important tools. Though Lean concepts are clear and practical, putting them into place is not so simple. It takes education, time, management systems, and lots of respect all around. Ultimately, sustainable improvement is enabled by educating and empowering your workforce.
Getting Started with OEE
Understanding losses with reliable OEE measurement systems is a necessary tool to drive operations improvement in manufacturing. For maximum business benefit, we must tie this understanding into our planning systems. This approach allows manufacturing companies to confidently evaluate and prioritize improvement efforts, which enables everyone to improve customer service and reduce inventory. Taking the right steps early in your initiative will help your organization avoid speed bumps:
- STRIVE TO ALIGN | Understand the organization’s interest level in OEE and improvement, and what is driving that interest.
- DOCUMENT THE CURRENT STATE | What operations metrics does your company currently use to measure productivity, and how do those measures differ from OEE?
- ENGAGE AND EDUCATE | Determine who will use OEE and how each role will use the underlying data to drive improvement.