Maximize the Value of Transformation Investments with Effective Change Management
Align people, processes, and technology for the greatest impact and sustainable value from digital transformation projects and investments.
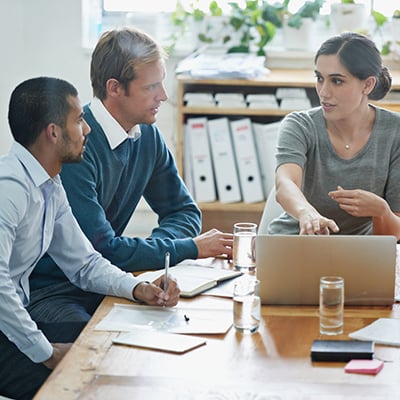
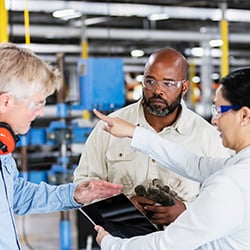
Trusted by these companies


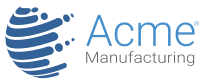
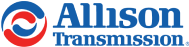
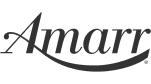
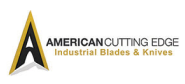
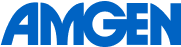
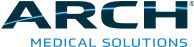
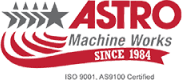
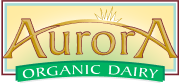
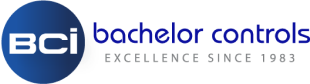

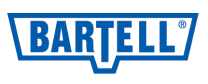


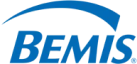



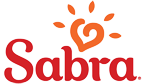
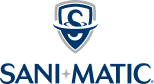

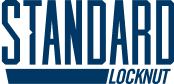

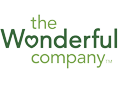

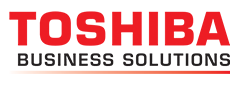
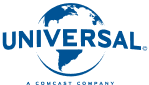

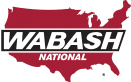
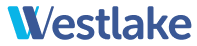
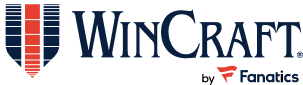


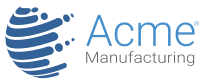
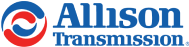
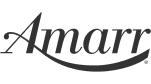
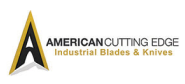
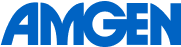
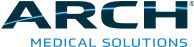
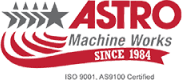
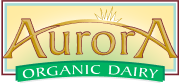
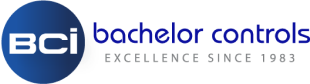

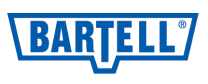


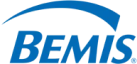



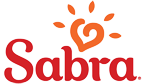
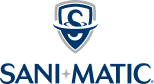

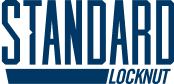

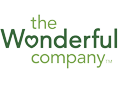

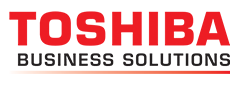
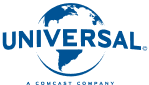

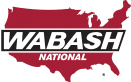
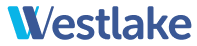
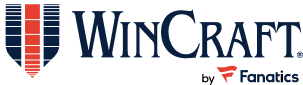


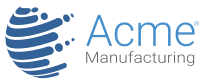
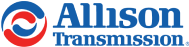
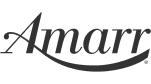
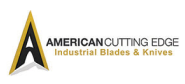
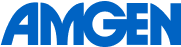
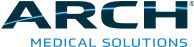
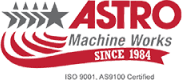
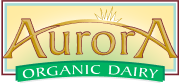
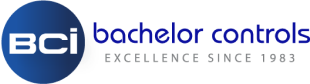

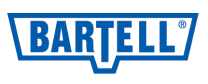


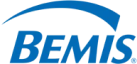



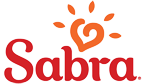
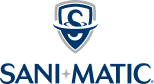

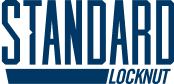

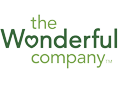

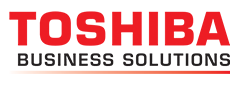
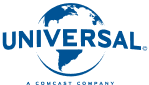

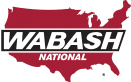
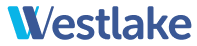
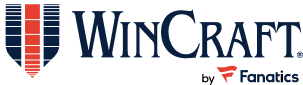
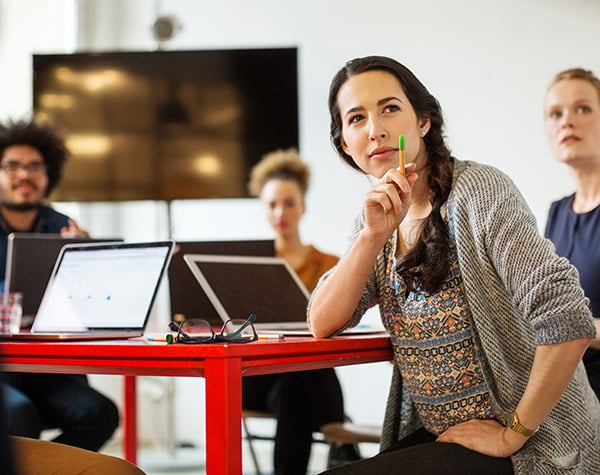
Create a culture of innovation and continuous improvement
You want your organization to be as dynamic as your business, customers, and industry. People are a critical part of your organization, and establishing the right culture helps everyone throughout your company eliminate waste, seek innovation, and improve performance. Sustainable change management enables you to:
- Spark employee engagement
- Foster teamwork and continuous improvement
- Inspire and empower innovation
- Deliver sustainable value and business results from digital transformation investments
Conduct technology projects that deliver business results
Every transformation project should address change from establishing the vision, to the first kickoff meeting, through system go-live, and throughout the entire lifecycle of the technology platform. Our manufacturing and supply chain consultants show your team how to create proper alignment across people, processes, and technology to make the best use of all your company’s resources.
- Business objectives and executive vision
- Technology requirements
- Project goals and expectations for outcomes
- Implementation requirements planning
- Go-live and training
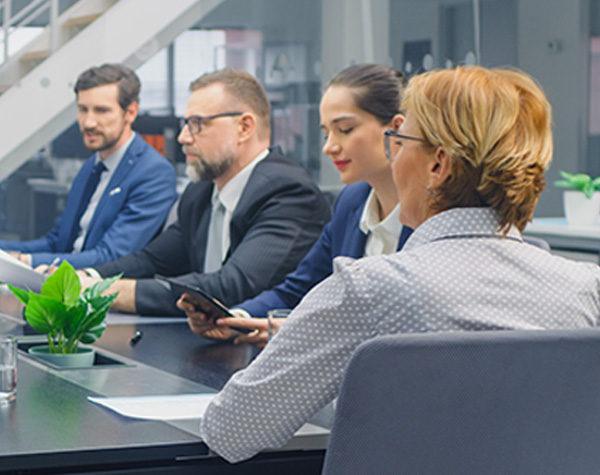
Choose the right continuous improvement style and process for your business
If your company is investing in continuous improvement, you want a scalable, repeatable program that gets results. When your company puts the the right CI process in place it has the ability to iterate to increase agility, reduce waste, increase efficiency and productivity, improve product quality, and decrease costs.
We specialize in continuous improvement for manufacturing and supply chain and can help your company determine which CI processes are right for your specific operations:
- Theory of Constraints, drum-buffer-rope
- Lean, SixSigma
- VITA analysis
- Deming Cycle, PDCA
- Kaizen: 5S, 5 whys, Kanban
Create and sustain enthusiasm for ongoing improvement with a center of excellence (COE)
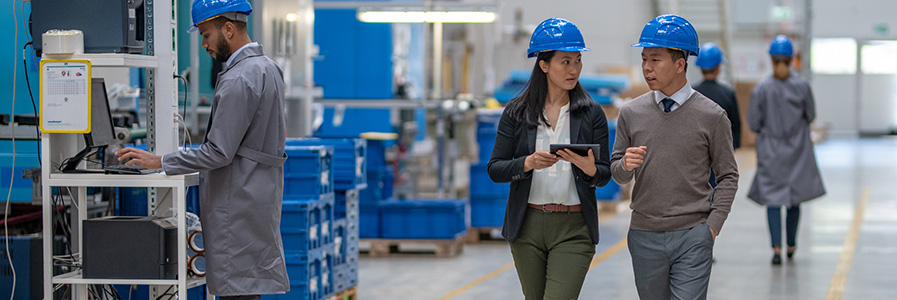
Drive standardization with a COE
Is your organization eager to maximize the impact of digital transformation? Creating a center of excellence (COE) for supply chain, manufacturing operations, production scheduling, or other disciplines is a unified way to set standards, drive continuous improvement, provide ongoing training, and cultivate innovation across the global enterprise.
Manufacturing companies view a COE as a practical way to:
- Standardize best practices, metrics, and goals
- Drive adoption
- Cross-train team members
- Create collaboration and assistance across sites
- Gather learnings and create a positive feedback loop
- Provide training, help, and resources
- Establish or contribute to the feedback loop for manufacturing processes and business processes
- Provide thought leadership and direction
Position COE for long-term success
Creating a center of excellence around a specific discipline like production scheduling, supply chain, or manufacturing operations is more than just organizing subject experts. Gathering the right people and setting a vision for broad disciplinary excellence is just the beginning of a COE endeavor. A company can position its scheduling COE for long-term success by adopting a progressive lifecycle: each phase builds on the success of preceding activities. Our change management experts and subject matter consultants guide your team throughout the COE lifecycle:
- Establish a foundation for an effective COE
- Focus first on low-hanging fruit
- Leverage early wins to expand focus
- Sustain enthusiasm for ongoing improvement
Keep your continuous improvement program going strong
Companies that invest in continuous improvement program understand that it’s not a “one and done” effort. Ideally, your company will conduct periodic reviews to ensure leaders and employees are aligned, engaged, and achieving higher levels of performance. Our continuous improvement experts partner with your team to objectively assess your CI process and create a roadmap for sustainability. We conduct an assessment to answer strategic questions about your existing CI program:
- Does existing technology support the CI program and delivering expected results?
- Does the CI program still reinforce business objectives?
- Is there still proper alignment across people, processes, and technology to make the best use of resources?
- Has the organization formalized the continuous improvement program and consistently apply CI best practices?
- Is the continuous improvement program embedded into the corporate culture, or was it put in place alongside an existing culture?
- Is the CI program scope too narrow or restrictive? Does it limit focus to only shop floor metrics instead of broad operational results like customer satisfaction, supplier relationships, inventory or supply chain performance, and other business objectives?
Partner with continuous improvement experts to identify gaps, explore program enhancements, and create a roadmap to ensure a sustainable continuous improvement program.
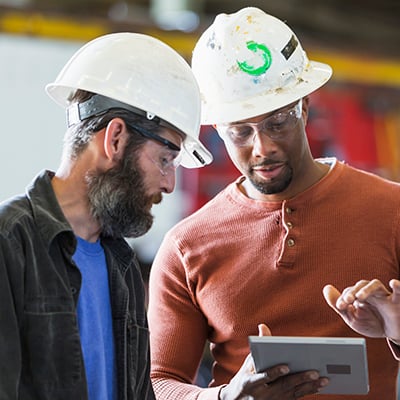
Helpful Resources
Get the value you expect from transformation, quickly and sustainably.
Digital transformation is our business. We are experts at deploying and integrating supply chain solutions and smart manufacturing systems – on time and within budget.
-
Digital transformation experts
-
Manufacturing and industry experts
-
Proven methodology
-
Change management