Create Workforce Alignment so Technology Investments Deliver the Results you Expect
Get people ready for transformative change.
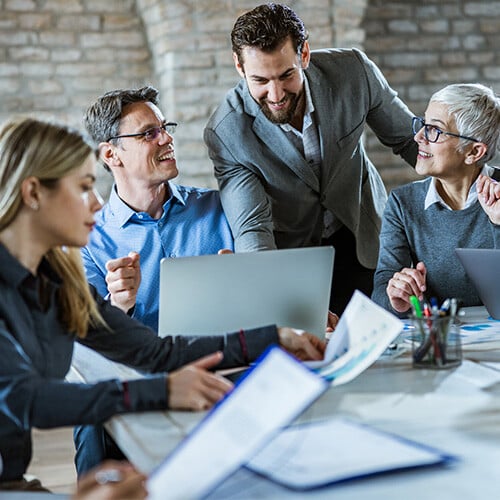
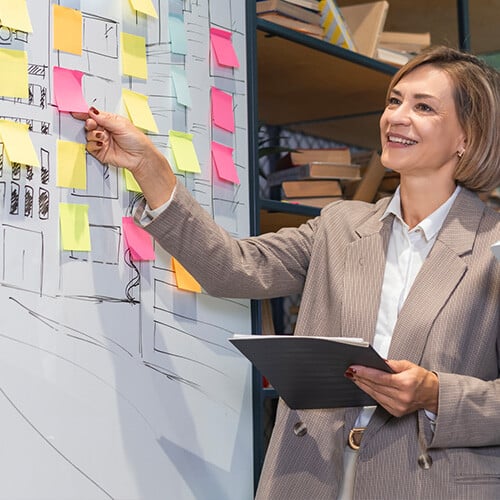
Trusted by these companies


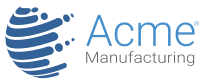
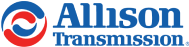
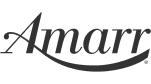
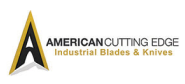
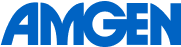
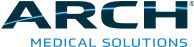
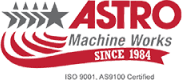
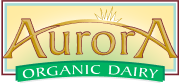
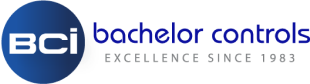

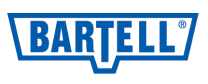


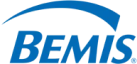



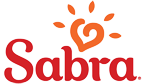
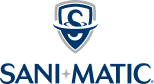

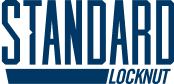

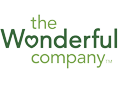

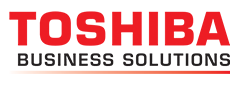
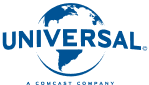

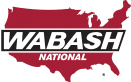
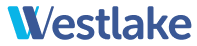
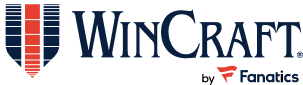


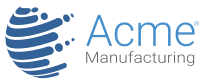
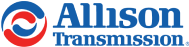
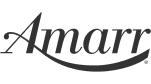
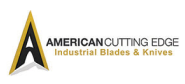
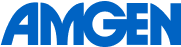
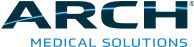
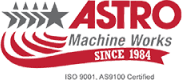
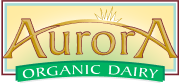
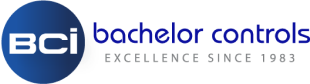

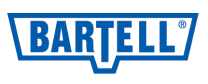


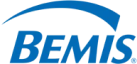



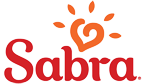
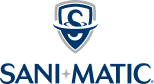

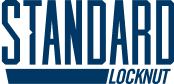

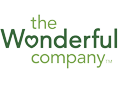

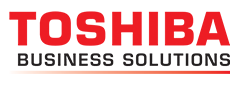
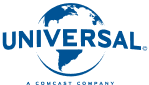

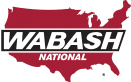
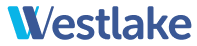
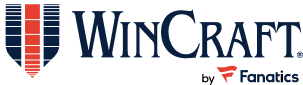


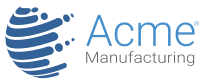
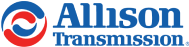
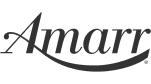
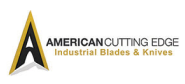
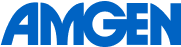
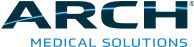
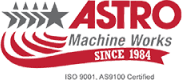
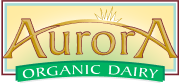
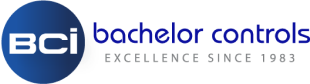

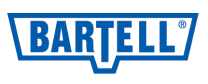


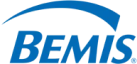



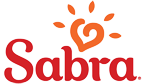
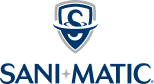

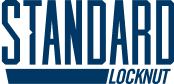

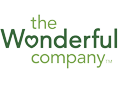

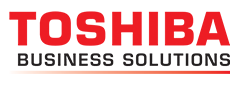
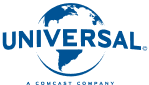

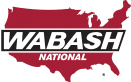
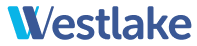
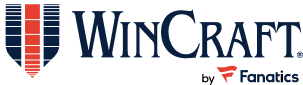
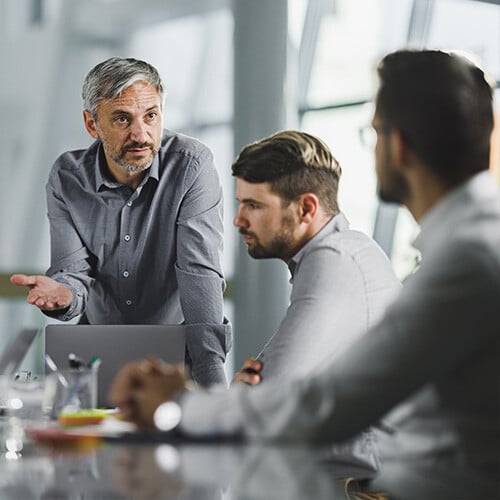
An outdated change management strategy could undermine your tech investments
A textbook change management strategy often falls short in building technology adoption or delivering business value. Yet, senior operations and finance executives invest in digital transformation specifically for the business results it can deliver.
If organization leaders expect a new system or process to drive value, it’s not enough to just “explain and train.” What the company needs is for employees to eagerly embrace the change and view it as something beneficial in their role or daily work routine.
A modern digital transformation initiative calls for an adaptive approach that combines elements of traditional change management with employee empowerment, leadership engagement, and a genuine focus on creating a shared vision of success.
This mutual perspective—cultural alignment—means transforming mindsets and building a future-ready organization.
Workforce alignment reduces risk and accelerates business impact
If your company is thinking about investing in a new system, the leadership team is making the investment with specific business goals in mind. It’s imperative to get system users and cross-functional teams aligned in support of your business objectives. Workforce alignment reduces risk and accelerates time-to-value associated with technology investments. It ensures that employees are working cohesively toward shared goals and partnering with leadership to:
- Eliminate inefficient, disconnected processes
- Identify and incorporate tribal knowledge
- Bridge current processes to more efficient processes using existing or new systems
- Create enthusiasm to drive faster adoption and value
- Preemptively address skills gaps
- Determine potential implementation barriers
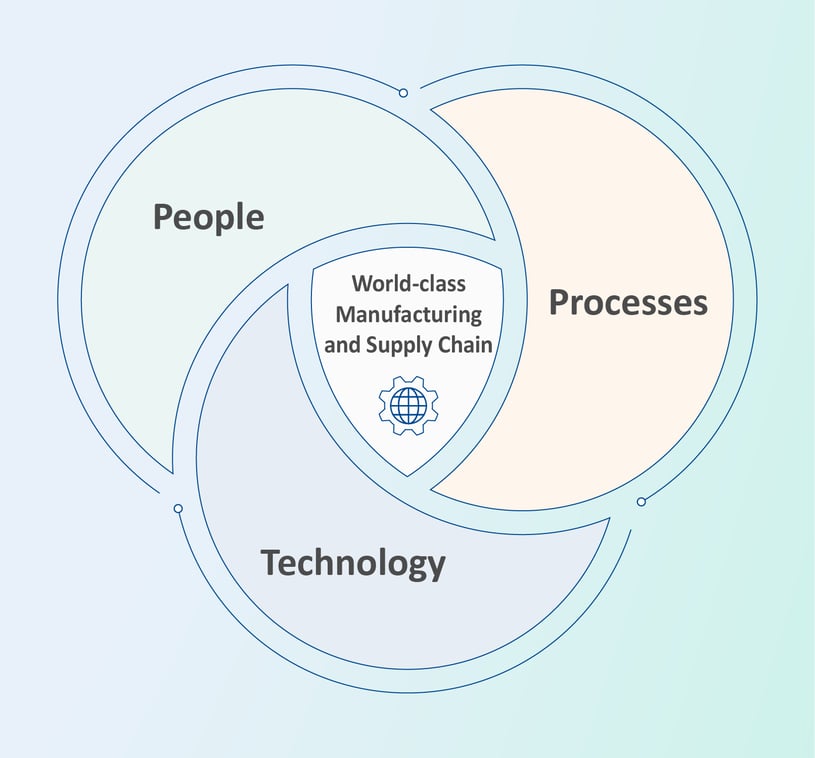
Lay the right groundwork so everyone can contribute to making change happen
Our tailored workshops are designed to break down barriers, create consensus, and establish the foundation for lasting change. We guide you in building the right foundation so that process and technology changes contribute to greater business success, instead of becoming an unwelcome distraction to your teams.
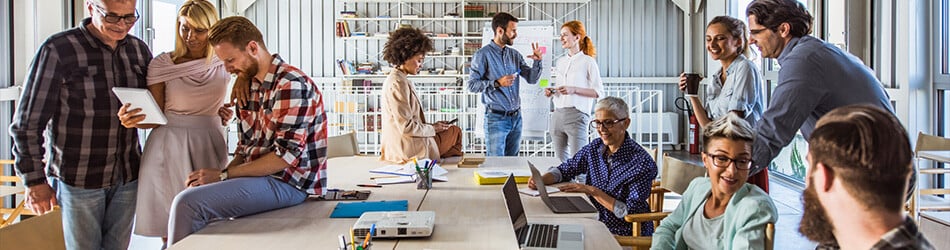
Critical outcomes you can expect
Align your workforce — Foster cross-functional collaboration and secure buy-in for process and technology changes.
Break down barriers — Guide candid conversations about change and identify obstacles to overcome.
Build cultural readiness — Empower your team to embrace innovation and take an active role in executing priorities.
Enhance efficiency — Identify bottlenecks, simplify processes, and prepare to leverage technology for better decision-making.
Unrivaled expertise and program design
- Industry-specific and discipline-specific change management experts
- Interactive workshop designed for active involvement
- Collaborative problem-solving to identify bottlenecks and efficiency opportunities
- Interactive sessions based on Theory of Constraints
- Practical activities illustrate the effects of various strategies on efficiency
- Onsite in your facility for maximum team accessibility
Learn how a workshop can help you build the right foundation for change
-
Duration: 3 days
Location and involvement: Each production plant
This high-performance workshop is specifically designed for cross-functional teams involved in keeping the factory running smoothly on a day-to-day basis. The On Time Edge Manufacturing Workshop examines throughput for a single plant including equipment, material, and processes. The team will explore how things work in their plant compared to how they *should* work, and build consensus around opportunities and changes needed.
Roles that typically participate include:
- Shift supervisors
- Plant manager
- Production schedulers
- Production planning
- Demand planning / order processing
- Purchasing
- Engineering
- Maintenance supervisor(s)
- Quality director
- Manufacturing IT director
- VP of operations or COO
What to expect during this workshop:
- Capture plant and function-level process information
- Document problems / challenges associated with each operational function
- Identify function-level business impacts
- Determine opportunities for improvement (process, by function, gaps, etc.)
- Illustrate the relationship between improvements and existing or potential systems
- Conduct production simulation
- Finalize three-year roadmap and financial projections with senior management team
-
Duration: 3 days
Location and involvement: Varies
Depending on how your company manages the supply chain, workshop is conducted at the corporate level, division level, or plant level.
This high-performance workshop is specifically designed for teams involved in supply chain orchestration, including medium-term and long-term planning:
- Strategic planning: 1-5 year horizon
- Tactical planning: 12-24 month horizon
The On Time Edge Supply Chain Workshop examines demand planning (forecasting), inventory planning, supply planning, capacity planning, and S&OP. The team will explore how things work in their organization compared to how they *should* work, and build consensus around opportunities and changes needed.
Roles that typically participate include:
- Supply chain director
- Supply chain planner(s)
- Demand planner(s) / forecasting
- S&OP manager / director
- Inventory manager / material planner
- Quality director
- Procurement managers
- Logistics coordinator
- Warehouse / DC manager
- VP finance or CFO
- VP of operations or COO
- VP of supply chain
What to expect during this workshop:
- Capture three-year outlook for business growth
- Document problems / challenges associated with each function
- Identify function-level business impacts
- Determine opportunities for improvement (process, by function, gaps, etc.)
- Illustrate the relationship between improvements and existing or potential systems
- Conduct supply chain management simulation
- Finalize three-year roadmap and financial projections with senior management team
Your workshop, tailored for your organization
Every business faces unique challenges, not just the “usual” problems seen by your industry. Your organization operates within a distinct set of circumstances, shaped by factors such as size, goals, geographic location, customer base, and organizational culture.
Even companies in the same industry encounter vastly different challenges because no two organizations share identical histories, strategies, or market dynamics. While one facility might grapple with staffing shortages or older equipment, another might face unusual supply chain disruptions or burdensome regional regulatory hurdles. These nuances mean every company navigates a unique path to success.
Our approach is a workshop tailored specifically for your organization’s unique concerns:
Curated content
Every workshop and the agenda tailored to address your specific organizational challenges.
Interactive exercises
Practical activities that illustrate the impact of various strategies on efficiency.
Collaborative problem-solving
Cross-functional teams working together to identify opportunities for improvement.
Expert facilitation
Industry-specific change management experts guide your team through the experience.
Get people aligned so your transformation investment delivers expected business results.
Workforce alignment bridges the gap between technology potential and practical implementation, so your investment achieves the intended outcome. Our experts help you:
- Create consensus for the changes required to achieve desired business results
- Get workforce aligned with process and technology in support of business objectives
- Secure buy-in for process and technology changes
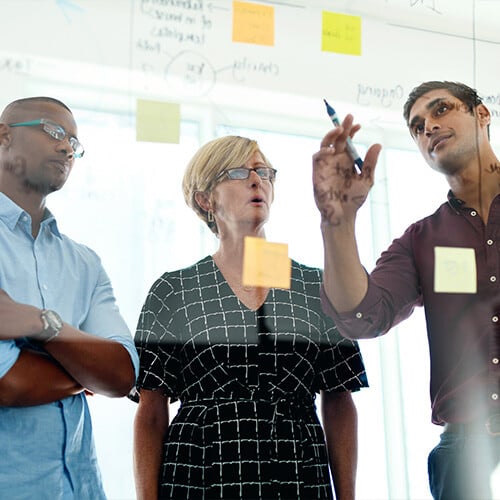
High-performance workshop prepares your workforce for transformative change
When we conduct a high-performance workshop with your team, we help them identify opportunities for improvements in product flow and costs. We guide the group as they explore how capacity management, material flow, bottlenecks, and demand planning affect business performance. Participants will also have an opportunity to examine the relationship between their performance and the company’s critical KPI’s.
Learn MoreUnlock your organization’s full potential with interactive, hands-on exercises that simulate real-world scenarios.
- Start candid conversations about change
- Validate that the coming change(s) will have the impact you expect
- Identify and build agreement about barriers to change
- Lay the groundwork for organizational readiness for transformative change
- Illustrate the benefits of change and foster workforce enthusiasm for change
- Encourage clear, unified communication for cross-functional teams
- Build a foundation for a culture of innovation and open dialogue
- Identify ways to simplify processes and enhance effectiveness
- Secure support for automating routine tasks and leveraging technology for better visibility
- Empower the workforce to take an active role in executing priorities
After carefully considering the elements that contribute to your business’ success, the workshop shifts to a review of the systems available and why they are necessary but not sufficient. Your consultant will also make recommendations about changes your team can make to improve operations with and without software. After the workshop, our team will help your leadership team establish a three-year roadmap with improvements and financial impact projections.
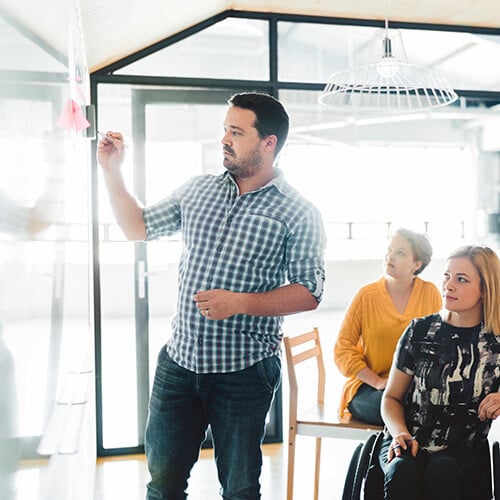
Every workshop tailored for your organization's unique concerns
Duration: 3 days
Location and involvement: Each production plant
This high-performance workshop is specifically designed for cross-functional teams involved in keeping the factory running smoothly on a day-to-day basis. The On Time Edge Manufacturing Workshop examines throughput for a single plant including equipment, material, and processes. The team will explore how things work in their plant compared to how they *should* work, and build consensus around opportunities and changes needed.
Roles that typically participate include:
- Shift supervisors
- Plant manager
- Production schedulers
- Production planning
- Demand planning / order processing
- Purchasing
- Engineering
- Maintenance supervisor(s)
- Quality director
- Manufacturing IT director
- VP of operations or COO
What to expect during this workshop:
- Capture plant and function-level process information
- Document problems / challenges associated with each operational function
- Identify function-level business impacts
- Determine opportunities for improvement (process, by function, gaps, etc.)
- Illustrate the relationship between improvements and existing or potential systems
- Conduct production simulation
- Finalize three-year roadmap and financial projections with senior management team
Duration: 3 days
Location and involvement: Varies
Depending on how your company manages the supply chain, workshop is conducted at the corporate level, division level, or plant level.
This high-performance workshop is specifically designed for teams involved in supply chain orchestration, including medium-term and long-term planning:
- Strategic planning: 1-5 year horizon
- Tactical planning: 12-24 month horizon
The On Time Edge Supply Chain Workshop examines demand planning (forecasting), inventory planning, supply planning, capacity planning, and S&OP. The team will explore how things work in their organization compared to how they *should* work, and build consensus around opportunities and changes needed.
Roles that typically participate include:
- Supply chain director
- Supply chain planner(s)
- Demand planner(s) / forecasting
- S&OP manager / director
- Inventory manager / material planner
- Quality director
- Procurement managers
- Logistics coordinator
- Warehouse / DC manager
- VP finance or CFO
- VP of operations or COO
- VP of supply chain
What to expect during this workshop:
- Capture three-year outlook for business growth
- Document problems / challenges associated with each function
- Identify function-level business impacts
- Determine opportunities for improvement (process, by function, gaps, etc.)
- Illustrate the relationship between improvements and existing or potential systems
- Conduct supply chain management simulation
- Finalize three-year roadmap and financial projections with senior management team
Helpful Resources
Get the value you expect from transformation, quickly and sustainably.
Digital transformation is our business. We are experts at deploying and integrating supply chain solutions and smart manufacturing systems – on time and within budget.
-
Digital transformation experts
-
Manufacturing and industry experts
-
Proven methodology
-
Change management