Over the years, our smart manufacturing consultants and systems engineers have narrowed down the top three reasons why manufacturing companies say they turn off OEE software:
- Not enough data - Some OEE systems take up too much operator time to collect data and enter it into the system. Data is often spotty or inaccurate, making the OEE software useless.
- No ownership - Whoever put the OEE software in place moved on, either within the organization or left the company altogether. When there's no one to provide oversight, OEE software use and value can deteriorate quickly.
- Not aligned - When the OEE software doesn't display metrics in a way that's useful and actionable to the people on the shop floor, they'll ignore it. This happens when things are too complicated or the metrics aren't right for the plant's industry.
OEE software that doesn't have enough data, lacks ownership, or isn't a good fit for the kind of manufacturing happening, won't be used to full potential or even worse, gets turned off. While these issues are often intertwined, any manufacturing company can tackle them one at a time.
But First, What is OEE Software?
OEE software (overall equipment effectiveness) software is a type of manufacturing execution System (MES) that's used to measure and track OEE. OEE is a metric that captures how well your manufacturing equipment is utilized and how often it produces good quality products. OEE takes into account three factors:
Availability: machine runtime divided by planned production time
Performance: ideal cycle time multiplied by total count, then divide by runtime
Quality: divide good parts by total parts produced
Align OEE Software with the Business
OEE software should be used to support the business, not the other way around. If the OEE system is already in place, the company can evaluate if it's still the right fit for the work taking place in the plant. (One way to do that is to check if your system can capture downtime reasons for your specific business.) If it's not, then it might be time to determine if a simple software re-configuration will help, or if the plant should shift to a different solution. With so many smart manufacturing cloud apps on the market today, making a switch isn't as painful as even 2-5 years ago.
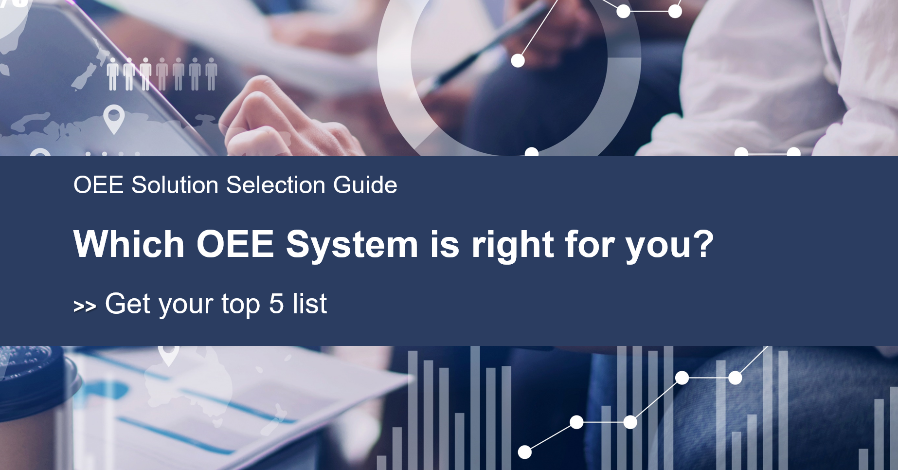
Identify Executive Sponsor for OEE Program
When production OEE software has no clear ownership, it's only a matter of time before things start to unravel. At minimum, the OEE system needs an executive sponsor. Ideally though your company would have an OEE center of excellence (COE), a cross-functional team that understands how OEE can help the company meet business goals and strives to make that a reality. The individuals don’t all need in-depth knowledge about system architecture, data protocols, or even change management. Each person would bring their own expertise and insight to the table. Collectively the group should have a determination and the authority to guide the initiative, whether it’s a continuous improvement program, part of a greater overall smart manufacturing initiative, or some other kind of plan. Their mission is to ensure the company gets maximum value from the production OEE software.
Accurate Data for OEE Software without Operator Input
OEE software needs data to produce results and it should make the operators' jobs easier, not harder. Companies have struggled to find a way to capture the right data, at the right time with as little disruption to production as possible. Automated data collection for OEE, MES, and ERP systems has come a very long way in the last 24 months. There are now OEE software data collection methods that don't require any operator input and can be used with any OEE system. This is a game-changer for OEE software because it means that any company can collect accurate data for smart manufacturing automatically without interrupting production.
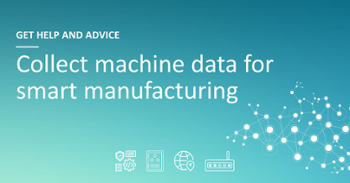
Don't Turn Off your OEE Software (yet)
If your OEE system is already off or you're not getting enough value out of it, your company can fix the problem with a little effort.
- Ask a few tough questions: Is it the right OEE software for us? Is it configured properly? If the answer to either of these questions is "no," then take a step back by either getting the right system or the right configuration in place. You might even want to step back a little further to understand what the company wants to accomplish by using OEE software. If the solution doesn't support your industry and your initiatives, your people won't use it.
- Make sure all the right people are involved. Even a mid-size company or plant can benefit by creating a collaborative team that represents a cross-section of roles and levels. An executive sponsor for this team might be an operations manager, CI director, or someone with visibility and authority at a corporate level. Whoever it is should clearly understand and support business objectives and remain cognizant and support the needs of the plant workforce.
- Consider automated data collection for complete, accurate data. Your OEE software needs accurate data to get the results needed. Find an OEE data collection method that doesn't require operator input and can be used with any OEE system. This is a game-changer for OEE software because it means that any company can collect accurate OEE data automatically without interrupting production.
Don't give up on OEE software just yet. With a little attention in the right ways, you can turn it around into a valuable asset for your company.