Leverage machine data to fuel systems, performance, and programs
What can your company do with more machine data?
- Feed your manufacturing execution system (MES), manufacturing operations management (MOM), or OEE system
- Measure performance to fuel the continuous improvement program
- Establish more accurate OEE and expand capability to identify root causes and solve problems
- Feed other systems and platforms to compound the value of your investments
When there's a data gap to analyze CNC machine data
A lot of companies have machine data gaps that create significant lag times to access, analyze, and act on performance opportunities. Without full access to data from manufacturing equipment, shop floor operators and management teams can’t determine where they can impact quality, scrap, and downtime.
If the CNC machine has a serial port or Ethernet port, you might be able to start getting machine data today. This access point can serve as a gateway to unlock valuable insights and optimize operations performance. By leveraging the connectivity options provided by these ports, you can bridge the gap between data collection and actionable analysis, empowering your team to make informed decisions that drive efficiency and productivity. Don't let data barriers hinder your progress – take advantage of the technology at your disposal and harness the power of machine data to propel your business forward.
However, sometimes getting data isn’t as simple as plugging a serial cable or Ethernet cable into the machine. Machine connectivity is defined by the type of connection that is supported by the machine builder. If your organization is missing data from even a few machines, it’s probably not getting full business value from the manufacturing operations management (MOM), MES, OEE, or ERP systems.
- Most factories have a broad mix of newer and legacy manufacturing equipment, and few organizations know how to get all the data out of every machine on the shop floor
- A majority of machine buyers aren’t aware that machine data isn’t standard or easily accessible on new capital equipment – some machine makers even charge a premium to get access to machine data
- IT groups are usually eager to help get data out of machines, but their teams aren’t always familiar with every cabinet and every protocol on every machine
- Maintenance engineers are machine experts, not data protocol or architecture experts; they usually struggle to get machine data quickly and in a cost-effective manner
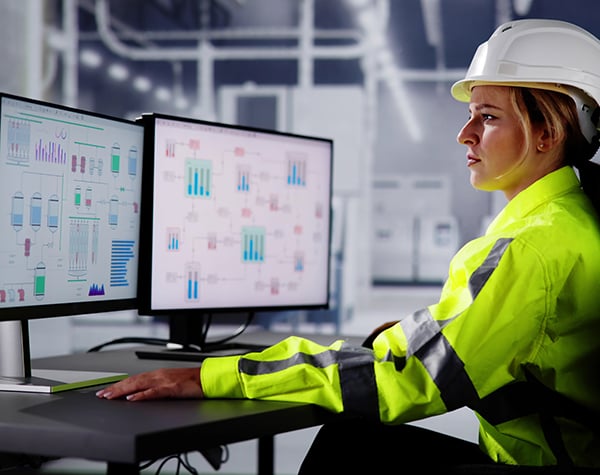
Vast landscape of machines, data sources, types of data
Our machine connectivity specialists understand machine and data protocols across >20 manufacturing industries, and have the right expertise to capture any kind of data from any data source.
Data sources
- Network or wireless devices (OPC, IP, Bluetooth, SPP protocols)
- Intelligent machines (PLC, CNC, CMM, robots, test stands, vision system, optical comparators)
- Local serial devices (micrometers, calipers, scales, tensile testers, hardness testers, keyboards, and other gauges via USB or RS232)
- Business systems (ERP, MES, LIMS, APC, HMI, SCADA, others)
- Existing data (ODBC databases, Microsoft Excel, structured text files)
Data types
- Quality measurements (weight, dimensions, functional tests)
- Process parameters (machine performance, environment)
- Attributes (visual inspections, defects)
- Traceability (tags, lot number, shift, machine)
We’ve seen every kind of machine and we get the data every time
Our proprietary machine connectivity audit is a proven methodology to document each asset’s “connectability,” (e.g., machine connectivity). It’s a critical foundational backbone for shop floor and manufacturing system projects and implementation so your team can create a dependable, achievable, and realistic project plan that includes every asset that is in-scope. Your machine connectivity expert will work with you to:
- Examine and document each asset’s “connectability,” (e.g., machine connectivity)
- Categorize machines into two groups (native connectivity such as FANUC FOCUS, MTConnect, Euromap 63, OPC, or OPC UA; or legacy equipment that require IIoT hardware or gateway device such as a PLC)
- Assess current connection state
- Capture all relevant machine information (location, serial number, brass tag info, controller, IP address, and many others)